Table of Contents
🔎 30-Second Summary
Tungsten is one of the few metals that defies engineering trade-offs — withstanding 3,422 °C, weighing more than lead, and resisting wear like diamond. This article explores how tungsten’s unmatched thermal and mechanical properties make it indispensable in aerospace, defense, nuclear power, and high-precision manufacturing. It also highlights global supply risks, India’s import dependence, and why recycling tungsten is becoming a key strategy in securing national technological resilience.
You’ve likely held tungsten in your hands today without knowing it — hidden inside your smartphone, powering the X-ray machine at your doctor’s office, or embedded in the cutting tools that shaped your car’s engine block. Yet tungsten remains one of the most strategically critical yet overlooked metals in modern technology.
What Makes Tungsten Unique
Withstanding temperatures of 3,422 °C (6,192 °F), tungsten possesses the highest melting point of any metal on Earth. This extreme thermal resistance, combined with a density of 19.25 g/cm³ — comparable to gold and 1.7 times denser than lead — creates a material unlike any other. When formed into tungsten carbide, it approaches diamond-like hardness, enabling applications where conventional materials simply disintegrate under pressure.
Key Properties That Define Tungsten’s Value
That rare combination of properties makes tungsten indispensable across industries most people never consider. From the plasma-facing walls of fusion reactors to the filament glowing in your desk lamp, from armor-piercing ammunition to the precision cutting tools that manufacture everyday products — tungsten operates in environments too hostile for virtually any other material.
“Tungsten combines unmatched heat resistance, ultra-high density, and near-diamond hardness — making it irreplaceable across sectors that operate under extreme stress.”
Why Tungsten’s Strategic Relevance Is Growing Globally
Yet tungsten’s strategic importance extends beyond its technical capabilities. With global supply chains concentrated in a handful of countries and applications spanning defense, aerospace, nuclear power, and precision manufacturing, this metal has quietly become a geopolitical asset. Nations recognize tungsten’s irreplaceable role in maintaining technological sovereignty and national security infrastructure.
This exploration reveals how tungsten’s extraordinary properties enable critical technologies across strategic sectors — and why securing reliable access to this remarkable metal has become a matter of national importance. In this article, we explore major and emerging tungsten uses across high-performance industries.
What Makes Tungsten Irreplaceable: Properties That Enable Impossible Applications
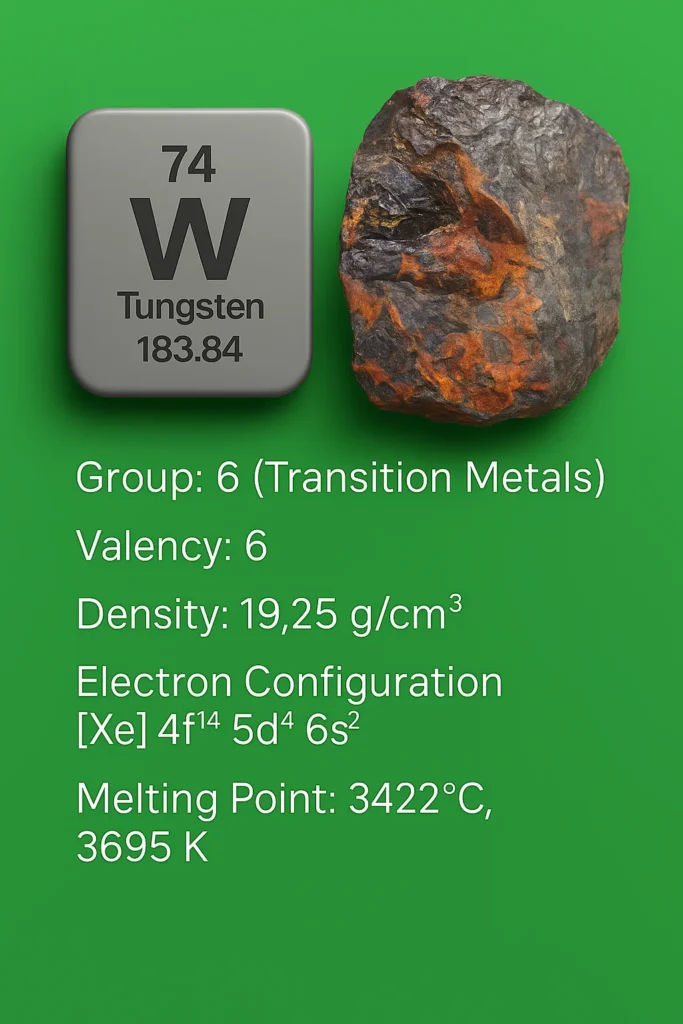
Tungsten’s atomic structure creates a perfect storm of properties found nowhere else in nature. While other metals compromise between strength and weight, or heat resistance and conductivity, tungsten defies these trade-offs entirely.
From aerospace to medicine, tungsten uses capitalize on extreme properties unmatched by any other element.
Extreme Thermal Resistance: Beyond the Melting Point
The most remarkable feature of tungsten material is its extraordinary melting point of 3422 °C (6192 °F) — a temperature that would vaporize most engineering materials. But tungsten’s thermal story goes deeper than raw melting point numbers.
Tungsten retains its structural strength at temperatures exceeding 1,650 °C, maintaining mechanical properties in environments where steel would flow like water. By contrast, nickel-based superalloys begin to lose strength around 1,000 °C, and even refractory metals like molybdenum deform well before tungsten’s limits. This thermal resilience stems from tungsten’s unique crystalline structure and strong metallic bonding, which resist the atomic vibrations that weaken other metals at high temperatures.
“Learning that tungsten stays strong at 1,650 °C—while most metals begin to soften—completely reframed how I understood high-temperature materials.”
Jet engine components, rocket nozzles, and plasma-facing surfaces in fusion reactors exploit this property, operating in thermal environments impossible for alternative materials.
Density Advantages: Maximum Mass in Minimum Space
With a density of 19.25 g/cm³, tungsten packs extraordinary mass into compact volumes. This density — 2.5 times that of steel and 1.7 times that of lead — results from tungsten’s tightly packed atomic arrangement and high atomic mass.
This puts tungsten in the same density class as gold — but unlike gold, tungsten resists deformation and heat. Compared to lead, it offers mass without toxicity, and compared to steel, it delivers maximum inertia in the smallest possible volume.
“Tungsten’s density isn’t just a statistic—it’s the hidden force behind stability in spacecraft, shielding in medicine, and impact in defense.”
Interestingly, this density changes with temperature, decreasing by approximately 5% at 1500°C and more than 15% near its melting point. This thermal expansion behavior remains predictable and manageable, unlike materials that undergo phase changes or structural failures.
How Tungsten’s Density Stacks Up Against Gold, Lead, and Steel
Metal | Density (g/cm³) | Tungsten Comparison | Primary Advantage |
---|---|---|---|
Tungsten | 19.25 | — | Maximum mass concentration |
Gold | ~19.3 | Nearly identical | Valuable but softer |
Lead | 11.3 | 1.7× lighter | Toxic, lower strength |
Steel | ~7.8 | 2.5× lighter | Much lower density |
Tungsten uses in industry capitalize on this density for counterweights in aerospace applications, radiation shielding in nuclear facilities, and ballast systems where concentrated mass improves performance.
Thermal Management: Conduction Without Expansion
Tungsten’s thermal conductivity of approximately 170 W/m·K makes it an exceptional heat conductor — crucial for applications requiring rapid heat dissipation. More importantly, its extremely low coefficient of thermal expansion (4.5×10⁻⁶ per °C) means components maintain dimensional stability even under severe thermal cycling.
That conductivity rivals metals like copper or silver, yet tungsten combines it with structural integrity those metals lack at high temperatures.
This combination proves critical in electronics applications. X-ray tube anodes must conduct heat away from the electron bombardment zone while maintaining precise alignment. Semiconductor interconnects need thermal stability to prevent connection failures as chips heat and cool during operation.
“Few metals conduct heat well without expanding. Tungsten’s low expansion coefficient helps it anchor systems where microscopic stability matters.”
The result: a material that efficiently transfers heat while maintaining microscopic tolerances — enabling technologies from medical imaging to advanced electronics.
Hardness and Wear Resistance: Approaching Diamond Performance
When combined with carbon to form tungsten carbide, tungsten approaches diamond-like hardness while retaining metallic properties like electrical conductivity and machinability. This transformation creates cutting tools that machine materials impossible to process with conventional steel tools.
The hardness results from tungsten’s ability to form extremely strong covalent bonds with carbon atoms, creating a crystalline structure that resists deformation and wear.
Unlike ceramic or diamond tools, tungsten carbide maintains toughness, conducts heat, and can be shaped using conventional metallurgy — giving it a trifecta of hardness, strength, and processability rarely found in one material.
Tungsten vs Key Alternatives
Property | Tungsten | Molybdenum | Lead | Nickel |
---|---|---|---|---|
Melting Point (°C) | 3422 | 2623 | 327 | 1455 |
Density (g/cm³) | 19.25 | 10.2 | 11.3 | 8.9 |
Toxicity | Non-toxic | Low | Toxic | Non-toxic |
Use Case | Fusion, Aerospace | Aerospace, Filaments | Shielding, Weights | Superalloys |
Key Takeaway: Tungsten’s unique combination of extreme thermal resistance, exceptional density, and dimensional stability creates capabilities no other material can match — enabling applications from spacecraft components to precision manufacturing tools that would be impossible with conventional materials.
Cost-Benefit Tradeoffs: Why Tungsten Wins Despite the Price
Tungsten is expensive, difficult to process, and heavier than most industrial metals — yet it continues to outperform alternatives where performance is non-negotiable.
Compared to cheaper materials like steel or aluminum, tungsten delivers durability, dimensional stability, and heat resistance that prevent system failure in mission-critical settings. In X-ray machines, for example, replacing tungsten with copper or graphite would reduce cost — but compromise precision and safety.
In high-speed CNC machining, tungsten carbide tools may cost 10–15× more than conventional steel cutters — but they last up to 80× longer and cut 4–7× faster, slashing both downtime and tool replacement costs.
Even in sectors like defense or satellite manufacturing, where every gram must justify its weight, tungsten’s unmatched density allows designers to concentrate mass where it’s needed most, reducing volume and improving efficiency.
“When reliability, longevity, or safety matter more than upfront cost — tungsten stops being expensive and starts being essential.”
Tungsten in Aerospace Engineering: High-Temperature and High-Density Applications

Aerospace engineering operates at the intersection of physics and national security, where material failures can mean the difference between mission success and catastrophic loss. Few metals can survive the extreme conditions of jet engines, spacecraft, and military systems — which explains why tungsten has become indispensable to aerospace applications worldwide.
Tungsten Alloys in Jet Engine Turbine Blades
Modern jet engines push materials to their absolute limits, with temperatures routinely exceeding 1000°C in turbine sections. Tungsten-containing superalloys provide the thermal stability required for reliable operation at these extreme temperatures. Modern turbine blades incorporate tungsten as an alloying element in concentrations of 1-3% by weight, where even small additions dramatically enhance creep resistance at elevated temperatures.
Just 2% tungsten addition to nickel-based superalloys can increase high-temperature strength by up to 30%, extending component lifespan in critical flight systems where failure is not an option.
Reading how just 2% tungsten in superalloys can boost strength by 30% revealed how even trace amounts shape mission-critical aerospace components
Radiation Shielding in Spacecraft Using W-Ni-Fe Alloys
Space presents unique threats that terrestrial materials rarely encounter. Cosmic radiation and solar flares can destroy sensitive electronics and endanger human life during extended missions. W-Ni-Fe alloys containing up to 90% tungsten create compact, effective shields against these hazards.
These dense materials protect both sophisticated electronics and human occupants while maintaining the machinability needed for complex spacecraft geometries. Weight constraints in space applications make tungsten’s exceptional shielding efficiency per unit volume particularly valuable.
“The use of tungsten-heavy alloys in space made me see how density isn’t just a number — it’s literal life support for astronauts and electronics.”
Counterweights and Ballasts in Satellite Systems
Satellite operation depends on precise weight distribution and stability control. Tungsten’s exceptional density enables gyroscopic stabilizers and counterweights that provide maximum mass in minimal space — a critical advantage where every cubic centimeter affects orbital mechanics and mission capability.
Tungsten’s density allows engineers to position mass precisely, a small cube can determine whether a satellite stays balanced in space
Tungsten Content in Functional Applications
Application | Tungsten Content | Key Benefit |
---|---|---|
Radiation Shields | 90-97% | Maximum protection per unit volume |
Counterweights | 92-96% | Optimal mass concentration |
Heat Sinks | 60-80% | High thermal conductivity with matched expansion |
W-Ni-Fe and W-Ni-Cu Alloys for Aerospace Structures
Tungsten heavy alloys (WHAs) combine density advantages with improved machinability, enabling specialized structural components where concentrated mass enhances performance. These materials serve dual purposes in many aerospace applications, providing both structural support and radiation attenuation capabilities.
I discovered tungsten alloys serve a double role, carrying structural load while quietly shielding vital electronics from radiation
Vibration damping systems particularly benefit from tungsten’s high density, which enables more effective control of mechanical resonances that could otherwise compromise mission-critical systems.
Heat Sinks and Thermal Management Components
Thermal management becomes crucial in aerospace electronics operating in extreme environments. Tungsten-copper composites featuring 60-80% tungsten content maintain dimensional stability while efficiently conducting heat away from sensitive components.
This combination of high thermal conductivity and low coefficient of thermal expansion prevents the thermal cycling failures that plague conventional materials in aerospace applications.
Key Takeaway: Aerospace applications exploit tungsten’s density and temperature resistance to create components that function reliably in environments where mission failure carries enormous strategic and economic consequences.
Tungsten in Nuclear Power and Radiation Systems
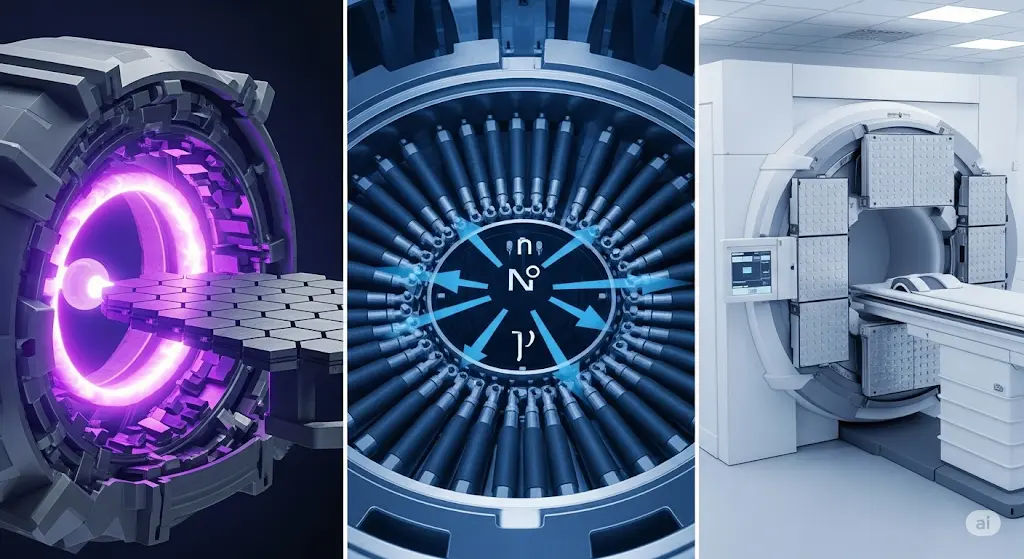
Nuclear reactors create conditions more extreme than almost anywhere else on Earth — temperatures reaching plasma temperatures exceeding 50 million degrees Celsius, neutron bombardment that would destroy most materials within minutes, and radiation levels lethal to humans. These environments demand materials with properties so extraordinary that only tungsten can reliably perform where everything else fails.
Tungsten as Plasma-Facing Material in Fusion Reactors
ITER (International Thermonuclear Experimental Reactor) represents humanity’s most ambitious energy project, and tungsten stands as its first line of defense against conditions that dwarf the sun’s core. Tungsten’s selection as the plasma-facing material stems from three critical properties: low hydrogen solubility, minimal sputtering yield, and its unmatched 3,422°C melting point. These characteristics enable tungsten to withstand plasma temperatures exceeding 50 million degrees Celsius while maintaining structural integrity.
The challenges remain formidable. Even tungsten undergoes surface modifications under such extreme conditions, including the formation of “fuzz” — microscopic fiber-like structures that develop under helium plasma exposure. This phenomenon demonstrates that while tungsten excels beyond any alternative, fusion energy pushes even this extraordinary material to its limits.
Learning that tungsten withstands 50-million-degree plasma revealed just how far material science must go to make fusion a reality
Fusion Reactor Divertors and Plasma-Facing Components
The divertor functions as a fusion reactor’s exhaust system, extracting heat and radioactive ash while protecting surrounding structures. ITER’s tungsten divertor components must endure heat fluxes of 10 MW/m² during steady-state operation and up to 20 MW/m² during transient events. The system transforms kinetic energy from plasma particles into manageable heat, then removes it through active water cooling.
These specifications highlight tungsten’s irreplaceable role: no other material combines the thermal capacity, dimensional stability, and radiation resistance required for this application.
“No other material matches tungsten’s balance of thermal load endurance and dimensional stability — it’s the unsung backbone of fusion reactor design.”
Material Performance in Fusion Environments
Material | Max Operating Temp | Neutron Damage Resistance | Tritium Retention |
---|---|---|---|
Tungsten | ~3400°C | Moderate | Very Low |
Beryllium | ~1287°C | Poor | High |
Carbon | ~3600°C | Good | Very High |
Tungsten Carbide in Reactor Core Components
Tungsten carbide delivers exceptional radiation shielding through its unique composition combining high-Z tungsten with low-Z carbon elements, providing superior attenuation of both neutrons and gamma radiation. While historically limited to space-restrictive applications, tungsten carbide increasingly appears in small modular reactor designs where shielding efficiency directly impacts reactor size and economics.
“Seeing how tungsten carbide shields against neutron and gamma radiation reframed how I think about reactor safety and size.”
Radiation Absorption in Nuclear Medicine Equipment
Medical applications showcase tungsten’s dual advantage over lead: 1.7 times higher density provides superior radiation protection while eliminating lead’s toxicity concerns. Nuclear medicine facilities rely on tungsten for syringe shields, collimators, and isotope containers where both radiation protection and personnel safety matter. The material’s exceptional attenuation properties enable thinner shields without compromising protection against gamma rays and X-rays.
Key Takeaway: Tungsten enables nuclear technologies that would otherwise remain theoretical — from fusion reactors pursuing clean energy to medical equipment saving lives — by functioning reliably in environments too extreme for any alternative material.
Tungsten Uses in Electronics and Electrical Devices

The tungsten filament glowing in your desk lamp represents one of the most enduring applications of this remarkable metal—a technology that sparked the modern electrical age and continues to power critical electronic systems today. Yet tungsten’s role in electronics extends far beyond simple lighting into sophisticated medical equipment, semiconductor manufacturing, and high-voltage power distribution.
Tungsten Filaments in Incandescent and Halogen Lamps
Hungarian Sándor Just and Croatian Franjo Hanaman received the first patent for tungsten filament lamps in 1904, launching a technology that significantly outperformed carbon predecessors. The breakthrough came from tungsten’s extraordinary 3410°C melting point, enabling filaments to maintain stability while glowing at operating temperatures of 2,500-3,000°C.
William D. Coolidge’s development of “ductile tungsten” through sintering in 1906 made practical filament manufacturing possible. Later innovations included inert gas filling with nitrogen and argon, which doubled luminous efficacy.
At working temperature, tungsten filament resistance increases to 12-15 times its cold resistance value. Modern halogen lamps exploit the “halogen cycle” where tungsten vapor chemically reacts with halogen gas, redepositing evaporated tungsten back onto the filament. This process extends lamp life and maintains envelope clarity despite extreme operating temperatures.
“Realizing tungsten survives while glowing at 2,500–3,000 °C made it clear why it still powers lighting after a century.”
X-ray Tube Anodes and Cathodes
Medical imaging relies extensively on tungsten’s unique properties for both anodes and cathodes in X-ray equipment. Tungsten’s high atomic number (Z=74) creates efficient bremsstrahlung radiation, while its 3370°C melting point withstands the intense heat generated during X-ray production.
“Tungsten’s high atomic number and heat tolerance make it central to the clarity and consistency of medical imaging.”
Modern X-ray tubes often utilize tungsten-rhenium alloys with a 90:10 ratio, as rhenium improves target durability. The anode body typically combines tungsten with lighter materials like molybdenum and graphite for optimal heat management.
Tungsten Interconnects in Semiconductor Devices
Semiconductor manufacturing depends on tungsten for critical interconnects in DRAM and 3D NAND memory systems. These components serve as word lines in DRAM, contacts in 3D NAND, and contacts in logic circuitry. However, tungsten interconnects may be approaching their performance limits, with molybdenum emerging as a potential successor.
“The more I studied semiconductor tech, the more tungsten appeared — silently enabling memory, storage, and logic layers.”
Tungsten-Copper Composites in Electrical Contacts
Electrical power systems rely on tungsten-copper composites that combine tungsten’s heat resistance with copper’s conductivity. Used primarily in circuit breakers and power switches, these materials operate reliably in vacuum, mineral oil, and SF6 gas environments.
“Tungsten-copper materials stood out for their ability to handle heat and conductivity where failure would cause blackouts.”
Material | Static Contact Resistance | Maximum Limit (IEC Standard) |
---|---|---|
W-Cu 75-25 | 0.08 mΩ | 0.2 mΩ |
W-Cu-Ni 75-24-1 | 0.11 mΩ | 0.2 mΩ |
High-Voltage Electrical Contacts
Power substations and industrial plants depend on tungsten-copper arcing contacts for high-voltage applications. The optimal tungsten content for minimizing arc erosion is approximately 80% by weight, though manufacturers adjust this between 60-90% depending on specific requirements.
Testing demonstrates these contacts maintain resistance values far below the 0.2 mΩ maximum specified by IEC 62271-100 standards. The addition of nickel to tungsten-copper materials improves mechanical properties through enhanced sintering.
Key Takeaway: Tungsten’s exceptional temperature resistance and electrical conductivity enable electronic components that function reliably under extreme conditions—from the century-old filament technology still lighting homes today to critical power distribution systems that keep electrical grids stable.
Tungsten in Defense and Military Engineering

Modern warfare has quietly become dependent on one of Earth’s rarest metals. Defense contractors and military planners recognize tungsten’s unique position: no other material combines the density, hardness, and thermal stability required for today’s advanced weapons systems and protective equipment.
Armor-Piercing Ammunition Using Tungsten Carbide
Tungsten carbide-cored ammunition represents a quantum leap in battlefield effectiveness. Modern 7.62x51mm projectiles with tungsten carbide cores demonstrate penetration capabilities approximately 1.9 times greater than NATO standard AP rounds when tested against hardened steel targets. The performance advantage becomes even more pronounced with larger calibers—12.7x99mm ammunition with tungsten carbide cores shows 150% improved penetration against ARMOX-500 steel alloy targets.
This superior performance stems from tungsten carbide’s exceptional hardness combined with tungsten’s 19.3 g/cm³ density. Unlike depleted uranium, tungsten carbide offers enhanced battlefield capabilities without radioactive concerns, making it increasingly attractive for military applications where environmental and health considerations matter.
“What struck me most was how tungsten outperforms depleted uranium—without the radioactive baggage.”
Kinetic Energy Penetrators and Shrapnel
Tungsten heavy alloys (WHAs) form the backbone of modern kinetic energy weapons. These W-Ni-Fe compositions containing 90-97% tungsten content deliver maximum impact energy through pure mass and velocity. Despite tungsten’s 3440°C melting point, powder metallurgy techniques enable processing at relatively manageable temperatures of approximately 1500°C when alloyed with nickel and iron.
“The idea that 90–97% tungsten alloys deliver lethal kinetic force made me realize mass itself can be a weapon.”
Alloy Type | Tungsten Content | Primary Applications | Key Advantage |
---|---|---|---|
W-Ni-Fe | 90-93% | Penetrators, ballasts | Superior penetration |
W-Ni-Co | 90-93% | Fragmentation munitions | Enhanced lethality |
W-Ni-Cu | 90-93% | Structural components | Corrosion resistance |
Radiation Shielding in Military Vehicles
Nuclear and radiological threats demand materials that provide maximum protection in minimum space. Tungsten’s exceptional density enables significantly thinner shielding compared to lead while delivering equivalent protection against gamma rays and X-rays. This weight and space efficiency becomes critical in military vehicles where mobility and protection must coexist.
“Tungsten protects soldiers not just with armor, but by enabling vehicles to stay agile and shielded at once.”
W-Ni-Fe and W-Ni-Cu Alloys for Structural Strength
These tungsten heavy alloys combine high density with excellent mechanical properties, creating materials ideally suited for defense applications requiring concentrated mass. The unique combination of density, mechanical strength, corrosion resistance, and formability makes them valuable for everything from armor systems to vehicle stabilization components.
Key Takeaway: Defense applications showcase tungsten’s strategic importance—its exceptional density and hardness create weapons that penetrate conventional armor and shields that protect against nuclear threats. Yet this dependence on such a geopolitically concentrated resource creates vulnerabilities that military planners must increasingly address.
Tungsten in Automotive and Industrial Machinery

Manufacturing precision separates good products from exceptional ones — and tungsten carbide cutting tools deliver that precision at speeds other materials cannot match. Beyond the factory floor, tungsten’s unique properties have found their way into the most demanding automotive applications, from Formula 1 racing engines to everyday CNC operations.
Tungsten Carbide Cutting Tools for CNC Machining
Tungsten carbide cutting tools dominate modern CNC machining operations, comprising more than 90% of turning tools and 55% of milling tools in some countries. These tools excel with their exceptional hardness, high strength, wear resistance, and superior elastic modulus—properties that make them indispensable for machining hard materials up to 50 HRC. The manufacturing process involves selecting qualified ground cut-to-length carbide rods, machining them according to specifications using 5-axis WALTER or ROLLOMATIC grinding machines, inspection, coating if necessary, and final testing.
Tungsten carbide tools cut at speeds 4-7 times faster than high-speed steel tools while lasting 5-80 times longer. This performance gap translates directly into manufacturing efficiency: reduced downtime, consistent part quality, and lower per-unit production costs. Machine shops processing hardened steels, titanium alloys, and exotic materials rely on tungsten carbide’s ability to maintain sharp cutting edges under extreme mechanical stress and thermal cycling.
“Learning that tungsten tools cut 4–7× faster and last up to 80× longer made me rethink what powers modern manufacturing speed.”
Engine Components: Crankshafts and Pistons
Formula 1 racing engines push materials to their absolute limits, where tungsten alloy crankshafts transform the piston’s reciprocating motion into rotation while providing crucial balance. Unlike traditional materials, tungsten alloys offer 60% higher density than lead and twice the density of steel, alongside superior hardness, wear resistance, corrosion resistance, and high-temperature stability. F1 racing engines frequently use tungsten alloy counterweights to balance the rotating inertia forces generated by connecting rod heads and crank journals, thereby ensuring smooth engine operation.
Alloy Type | Tungsten Content | Primary Applications | Key Advantage |
---|---|---|---|
W-Ni-Fe | 90-93% | Penetrators, ballasts | Superior penetration |
W-Ni-Co | 90-93% | Fragmentation munitions | Enhanced lethality |
W-Ni-Cu | 90-93% | Structural components | Corrosion resistance |
These engines operate at rev limits exceeding 15,000 RPM, where conventional counterweights would fail due to centrifugal forces. Tungsten’s exceptional density allows engineers to achieve perfect rotational balance with minimal mass, reducing bearing loads and extending component life even under extreme operating conditions.
“In racing engines spinning at 15,000 RPM, tungsten’s density becomes the key to balance, durability, and speed.”
Balancing Weights in High-Performance Vehicles
High-performance racing teams utilize tungsten heavy alloy for chassis and rail weights to achieve optimal weight distribution. With a density 150% that of lead, tungsten allows engineers to place small, high-mass components in precise locations, thus improving weight balance and maximizing performance. Importantly, tungsten alloy counterweights help reduce loads on parts, extending service life. These components are particularly valuable for race car ballast to meet minimum weight requirements in motorsport regulations like those set by the FIA.
Property | Tungsten Alloy | Steel | Lead |
---|---|---|---|
Density | 17-18.5 g/cc | 7.85 g/cc | 11.3 g/cc |
Toxicity | Low | Low | High |
Heat Resistance | Excellent | Good | Poor |
Race car engineers face a constant challenge: meeting minimum weight requirements while optimizing weight distribution for handling characteristics. Tungsten’s extraordinary density provides a solution that lead cannot match — concentrated mass that can be positioned exactly where needed without compromising aerodynamics or structural integrity.
Key Takeaway: Tungsten enables manufacturing precision and automotive performance that conventional materials cannot achieve — creating cutting tools that process the hardest materials at unprecedented speeds and racing components that function reliably at rotational forces that would destroy traditional alternatives.
Tungsten in Precision Manufacturing: The Metal Behind Modern Production
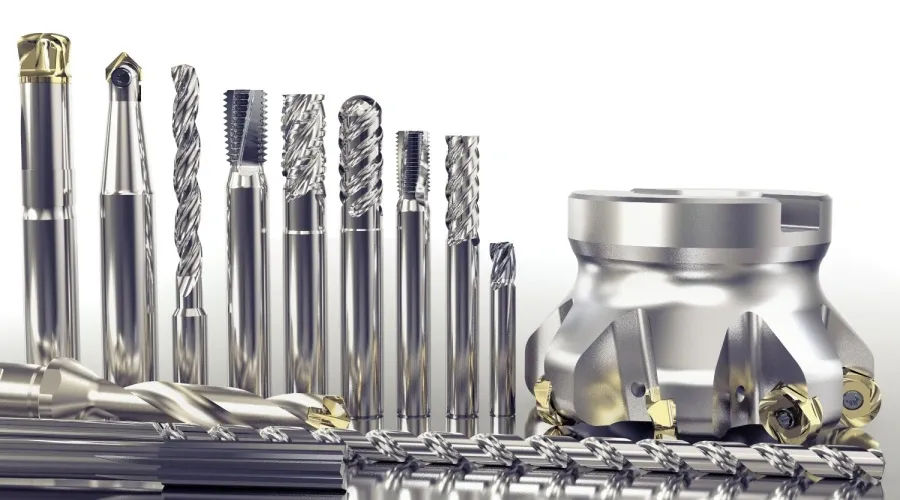
Modern manufacturing runs on precision — tolerances measured in micrometers, surface finishes approaching perfection, and tools that must perform consistently across thousands of operational cycles. Tungsten carbide has quietly become the backbone of this precision economy, enabling manufacturing capabilities that would be impossible with conventional materials.
Tungsten Carbide’s Dominance in CNC Operations
Tungsten carbide cutting tools command more than 90% of turning tools and 55% of milling tools in advanced manufacturing countries. This dominance stems from exceptional hardness, superior wear resistance, and an elastic modulus that maintains cutting edge geometry under extreme forces — properties that make tungsten carbide indispensable for machining hardened materials up to 50 HRC.
The manufacturing process itself demands precision: qualified ground cut-to-length carbide rods, machined to specifications using 5-axis WALTER or ROLLOMATIC grinding machines, inspection, coating when necessary, and final testing. Wire Electric Discharge Machining (WEDM) creates complex geometries that conventional machining cannot achieve.
Recent advances show zinc-coated brass wire delivers higher cutting speeds compared to uncoated alternatives when machining tungsten carbide. Multiple passes — typically four — produce surface finishes allowing manufacturers to hold ±0.0002″ tolerances even in 2″ thick carbide.
“When I read about ±0.0002″ tolerances, it became clear why tungsten carbide is trusted for parts that simply can’t fail.”
Tungsten carbide tools operate at 4-7 times the cutting speeds of high-speed steel while lasting 5-80 times longer. This performance gap explains why manufacturers invest in tungsten carbide despite higher initial costs — the productivity gains and extended tool life justify the premium.
Wire Drawing Dies: Where Tungsten Faces Its Toughest Test
Wire drawing operations present one of the most demanding applications for any material. Die costs alone account for over 50% of total wire drawing expenses, making die longevity critical for economic viability. Tungsten carbide dies face multiple wear mechanisms simultaneously: abrasion from the wire surface, adhesion between wire and die materials, thermal fatigue from repeated heating and cooling, and chemical corrosion from lubricants.
The industry has responded with advanced die technologies that push performance boundaries:
Die Type | Substrate | Relative Lifespan | Best Application |
---|---|---|---|
Tungsten Carbide | WC-Co | Baseline | Steel wire drawing |
Diamond Coated | WC-Co with CVD coating | 10× longer | Carbon & welding wire |
Polycrystalline Diamond | Artificial diamond | 15-25× longer | Fine wire drawing |
These performance improvements directly impact manufacturing economics. A diamond-coated die lasting ten times longer than tungsten carbide transforms the cost structure of wire production, enabling manufacturers to produce finer wires with better surface finishes at lower total costs.
“The fact that die costs dominate wire production showed me just how critical tungsten’s durability really is.”
Tungsten Coatings: Extending Mold Life by Orders of Magnitude
High-pressure die casting subjects molds to extreme conditions — molten metal temperatures exceeding 650°C, injection pressures reaching 150 MPa, and rapid thermal cycling that would destroy conventional materials. Tungsten-based pseudoalloys provide a solution that field testing validates dramatically.
Tungsten coatings can increase casting kernel lifespan by a factor of 20. The microstructure within these coatings determines both mechanical properties and corrosion resistance. Tungsten heavy alloys excel where molds must withstand the simultaneous assault of high-pressure molten metal impact, rapid thermal cycling, and potential chemical attack from aggressive alloy compositions.
This performance improvement transforms die casting economics. Molds lasting twenty times longer reduce replacement costs, minimize production downtime, and enable more consistent part quality throughout extended production runs.
Key Takeaway: Tungsten’s role in precision manufacturing extends far beyond simple hardness — its ability to maintain dimensional stability under extreme conditions enables the tight tolerances and consistent performance that modern manufacturing demands, from cutting tools that shape critical components to dies that must perform flawlessly across thousands of operational cycles.
Tungsten in Medical and Healthcare Engineering

Medical professionals depend on tungsten’s unique properties to deliver life-saving care while protecting themselves from harmful radiation. This metal’s combination of density, non-toxicity, and durability has quietly become essential to modern healthcare infrastructure.
X-ray and CT Scanner Shielding
Modern diagnostic imaging relies on tungsten’s exceptional radiation attenuation properties. In X-ray tubes, tungsten serves as both the cathode filament and the anode target, withstanding the intense heat generated during radiation production while maintaining structural integrity. For radiation shielding applications, tungsten alloy components in CT scanners provide superior protection compared to traditional lead-based systems.
Tungsten’s shielding effectiveness exceeds lead by more than 1.7 times under equal thickness conditions, with this advantage becoming more pronounced as radiation energy increases. This superior performance allows for thinner, lighter shielding components that improve equipment mobility and reduce installation constraints.
Despite tungsten’s slightly lower atomic number compared to lead, its significantly higher density creates more effective radiation barriers for modern medical imaging equipment.
Tungsten-Based Syringe Shields and Collimators
Nuclear medicine procedures require precise radiation beam control and worker protection. Tungsten heavy alloys form the core of multi-leaf collimators that shape radiation beams with millimeter-level accuracy during therapeutic treatments. These components must maintain dimensional stability while repeatedly directing high-energy radiation beams.
Healthcare workers handling radiopharmaceuticals rely on tungsten syringe shields for hand protection during injection procedures. These shields feature anodized aluminum exteriors to resist damage from accidental drops, combined with lead glass viewing windows for visual confirmation of dosage levels.
“Learning how syringe shields blend safety and precision gave me a new respect for how tungsten protects healthcare workers.”
Tungsten vs Lead in Healthcare: Safety, Durability, and Radiation Shielding Compared
Property | Tungsten | Lead | Healthcare Advantage |
---|---|---|---|
Density | Higher | Lower | Superior radiation attenuation |
Toxicity | Non-toxic | Toxic | Safer for healthcare environments |
Durability | Resistant to chips | Easily damaged | Better infection control |
Surgical Tools and Dental Drills with Tungsten Tips
Surgical precision depends on instruments that maintain sharpness through countless procedures. Tungsten carbide cutting edges and drill tips deliver exceptional hardness, strength, and corrosion resistance in demanding surgical environments. Clinical studies show surgical instruments with tungsten carbide inserts outlast standard instruments up to five times longer while maintaining superior cutting performance.
This extended service life translates directly to improved patient outcomes through cleaner incisions, reduced operating times, and faster healing rates. Dental applications particularly benefit from tungsten carbide’s ability to maintain precise cutting geometry even when drilling through the hardest tooth structures.
Key Takeaway: Tungsten enables life-saving medical technologies that protect both patients and healthcare workers—from radiation shielding that allows safer diagnostic imaging to surgical instruments that deliver precise treatment with minimal tissue damage.
Emerging Technologies: Where Tungsten Engineering is Headed
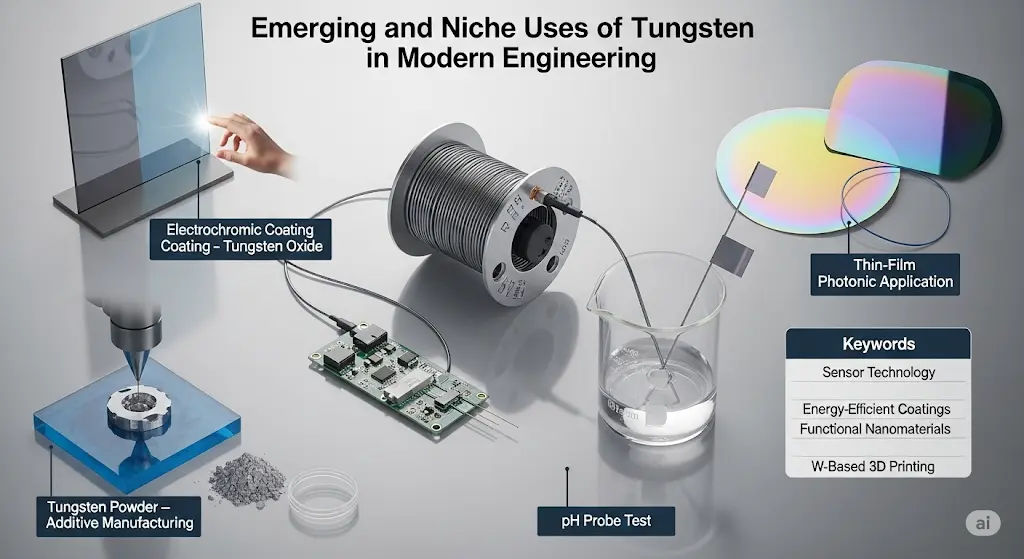
Tungsten’s extraordinary properties continue unlocking technological possibilities that seemed impossible just decades ago. These breakthrough applications reveal how material science boundaries keep expanding, with tungsten enabling innovations from nanoscale sensors to architectural energy systems.
Tungsten Nanowires in Sensor and pH Probe Development
The precision measurement revolution has found an unlikely champion in tungsten nanowires. When covered with their native oxide layer, these nanowires demonstrate remarkable sensitivity to pH changes, showing a linear response with R² values of 0.999 and sensitivity of -53.8 mV/pH. These sensors respond in less than 0.1 seconds with a functional lifetime exceeding 44 days.
What makes tungsten-based sensors extraordinary is their stability in hostile environments where conventional sensors fail completely.
Sensor Type | Response Time | pH Range | Key Advantage |
---|---|---|---|
WO₃ Nanoparticles | Under 0.1s | 5-9 | Sensitivity (-56.7 mV/pH) |
W/WOₓ Micro-sensor | Under 0.1s | Wide | Anti-interference (selectivity >7) |
Tungsten Nanowire | Quick | 2-11 | Stable in extreme environments |
Tungsten-based pH sensors maintain Nernstian response even at temperatures between 200-300°C, making them viable for extreme industrial environments where traditional sensors would be destroyed.
Tungsten in Smart Windows and Thin-Film Coatings
Electrochromic tungsten oxide (WO₃) coatings represent a breakthrough in building energy efficiency. These smart windows switch between transparent and tinted states with minimal power consumption, delivering 30-40% greater energy savings than conventional windows.
The mechanism relies on tungsten’s unique electrochemical behavior — WO₃ changes from colorless to dark blue when ions intercalate its structure, with the tungsten oxidation state shifting from 6+ to 5+.
HiPIMS (High-power impulse magnetron sputtering) technology produces optimized WO₃ coatings with superior coloration efficiency of 12.15 cm²/C for annealed films. These films withstand thousands of coloration-bleaching cycles with open-circuit memory exceeding three days.
Tungsten in Additive Manufacturing and 3D Printing
Additive manufacturing has cracked the code on tungsten’s notorious processing challenges, opening possibilities for complex geometries previously impossible to create. This advancement proves particularly valuable for fusion reactor components, specialized armor systems, and nuclear applications. Three main techniques now process tungsten successfully: laser powder-bed-fusion (L-PBF), laser directed-energy-deposition (L-DED), and electron beam powder-bed-fusion (EB-PBF).
Despite tungsten’s challenging combination of high melting point, exceptional thermal conductivity, and brittleness, recent technological breakthroughs have overcome these limitations. EBM (Electron Beam Melting) shows particular promise for manufacturing crack-free tungsten components by preheating the metal to prevent deformation and residual stresses.
A recent breakthrough by the Fraunhofer Institute demonstrated crack-free tungsten parts using EB-PBF for high-heat neutron shielding, showing >99% density and excellent dimensional tolerance. Similar techniques are being evaluated by CERN and Indian nuclear labs for advanced radiation shielding components.
Tungsten in Energy Storage and Supercapacitors
Tungsten compounds, especially tungsten oxide (WO₃), are gaining attention in energy storage for their fast redox kinetics and structural stability. Supercapacitors built with WO₃ electrodes have demonstrated higher energy densities and longer cycle lives than traditional carbon-based systems.
A 2022 study from the Indian Institute of Science showed that WO₃–graphene hybrids improved energy storage by 35% over conventional materials. These breakthroughs could enhance hybrid EVs, backup power systems, and grid-level storage solutions.
Case Study: Xiamen Tungsten / Lithium–Tungsten Hybrid Electrodes
Challenge: Improve energy density and cycling stability of lithium-ion batteries.
Tungsten Solution: Integrated tungsten oxide (WO₃) nanosheets into cathode material.
Results: Increased charge capacity by 35%, and improved thermal stability at 80°C+.
Source: ScienceDirect, 2023
Tungsten in Semiconductor Fabrication
Tungsten plays a crucial role in modern semiconductor manufacturing, where it’s used as a contact and interconnect material in CMOS devices. Tungsten deposition techniques — like CVD and atomic layer deposition — provide superior step coverage and resistance to electromigration, outperforming copper in nanoscale nodes.
Foundries like TSMC and Intel continue to rely on tungsten for gate fill and TSV structures in 5nm and below process nodes, where stability under thermal stress is essential for yield and performance.
Case Study: Intel / Tungsten Interconnects in 10nm Process Node
Challenge: Reduce RC delay and prevent electromigration in dense chip layouts.
Tungsten Solution: Replaced copper with tungsten for specific critical layers.
Results: Enhanced performance consistency and reliability over 10 billion cycles.
Source:IEEE IEDM 2022
Key Takeaway: Tungsten’s emerging applications demonstrate how extraordinary material properties enable breakthrough technologies — from nanoscale sensors operating in environments too hostile for conventional materials to smart building systems that dramatically reduce energy consumption and manufacturing techniques that create previously impossible component geometries.
Global Tungsten Supply and Strategic Trade
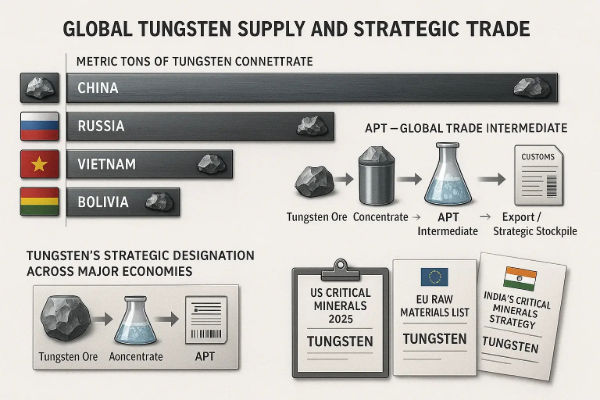
The global tungsten market operates as a complex geopolitical bottleneck, where supply concentration creates vulnerabilities that extend far beyond market economics. With applications spanning fusion reactors, armor-piercing ammunition, and precision manufacturing, tungsten’s strategic value has transformed it into a weapon of industrial diplomacy.
Major Producers: China, Russia, Vietnam, Bolivia
China’s overwhelming dominance in tungsten processing creates a strategic chokepoint that affects global industrial capacity. While other nations mine tungsten ore, China controls the critical intermediate processing that transforms raw materials into usable industrial products.
Country | Position in Global Supply | Primary Form | Key Characteristic |
---|---|---|---|
China | Dominant producer | APT, oxides, metal | Controls 80%+ of processing |
Russia | Second largest | Concentrates | Long-established mining sector |
Vietnam | Growing producer | Concentrates | Masan Resources expansion |
Bolivia | Emerging producer | Ore | Primarily from tin mining byproducts |
A single smartphone contains approximately 0.15 grams of tungsten, primarily in the vibration mechanism that makes your phone buzz. Yet this tiny amount represents part of a supply chain that could be disrupted by geopolitical tensions, trade restrictions, or processing capacity limitations.
Strategic Role of Ammonium Paratungstate (APT) in Global Trade
APT (ammonium paratungstate) serves as the “currency” of international tungsten trade, functioning as the primary intermediate compound that bridges raw ore and finished products. Nations controlling APT production effectively control access to tungsten-dependent technologies, from medical X-ray equipment to military targeting systems.
APT prices establish the benchmark for tungsten products globally, making this seemingly obscure chemical compound a lever of industrial influence. Countries dependent on tungsten imports find themselves vulnerable to supply disruptions that could cripple critical infrastructure and defense capabilities.
Tungsten’s Inclusion in Critical Mineral Lists Worldwide
The European Union, United States, Japan, and Australia have all designated tungsten as a critical material requiring supply chain risk mitigation strategies. These classifications acknowledge both tungsten’s irreplaceable role in national defense and the fragility of current supply arrangements.
Unlike commodities with multiple suppliers and substitute materials, tungsten’s unique properties create dependencies that cannot be easily resolved through market mechanisms. The metal’s applications in fusion research, precision manufacturing, and defense systems make supply security a matter of technological sovereignty.
Key Takeaway: Tungsten supply chains represent a strategic vulnerability for nations dependent on this irreplaceable metal, creating geopolitical leverage for producing countries and driving urgent efforts to diversify sources, develop recycling capabilities, and build strategic reserves.
Global Tungsten Consumption by Industry (2025)
In 2025, global tungsten demand is driven by a handful of key sectors. Electronics manufacturing remains the largest consumer, owing to tungsten’s critical role in semiconductors, filaments, and high-performance contacts.
Precision manufacturing (especially CNC cutting tools and wear parts) and aerospace applications also account for significant shares. Below is a breakdown of estimated world tungsten consumption by end-use industry:
Industry | Share of Total Consumption |
---|---|
Electronics & Electrical Devices | 32% |
Precision Manufacturing | 22% |
Aerospace Engineering | 15% |
Automotive & Industrial Machinery | 12% |
Defense & Military Technology | 9% |
Medical & Healthcare Applications | 5% |
Other (Energy, Additive Mfg, etc.) | 5% |
Key takeaways:
- Electronics leads by a wide margin, driven by continued growth in semiconductors, displays, and lighting technologies.
- Precision manufacturing (including cutting tools, dies, and wear-resistant components) represents the next largest tranche, reflecting the ubiquity of tungsten carbide in modern machining.
- Aerospace’s 15% share underscores tungsten’s irreplaceable role in high-temperature and high-density applications, from turbine components to satellite ballast.
- The smaller “Other” category captures emerging areas such as additive manufacturing, thin‐film coatings, and energy applications.
This consumption profile highlights where the bulk of tungsten is being applied today—and points to the industries that will most benefit from improvements in tungsten processing, alloy development, and recycling.
India’s Tungsten Reserves and Strategic Roadmap
India imports over 95% of its tungsten requirements — a dependency that creates strategic vulnerabilities precisely where this metal matters most. While the nation pursues ambitious goals in defense manufacturing, space missions, and advanced electronics, its tungsten supply chain remains dangerously concentrated in foreign sources.
Known Deposits: Degana, Chhattisgarh, Nagaland
The Degana belt in Rajasthan holds approximately 12.5 million tons of tungsten ore — India’s most significant known deposit. Yet this resource sits largely undeveloped, a reminder of how complex geology intersects with economic and strategic realities.
Other deposits scattered across Chhattisgarh and Nagaland’s Tuli region contain scheelite and wolframite minerals, though at concentrations that have historically proven challenging to extract profitably.
Tungsten Ore Deposits in India: Degana, Maharashtra, and Nagaland at a Glance
Location | Estimated Resources | Mineral Type | Development Status |
---|---|---|---|
Degana, Rajasthan | 12.5 million tons | Wolframite | Partially developed |
Kuhi-Khobna, Maharashtra | 0.2 million tons | Scheelite | Undeveloped |
Bruiamura, Nagaland | Under exploration | Wolframite | Exploration stage |
The Degana mines once powered India’s early lighting industry, producing tungsten for domestically manufactured light bulb filaments. Today, these same deposits represent untapped potential in a world where tungsten has become far more strategically critical.
Past Mine Closures and Exploration Challenges
Economic viability killed India’s tungsten mining operations. Faced with cheaper Chinese imports and rising extraction costs, the Degana mines closed , a decision that seemed rational then but creates strategic exposure now. Exploration efforts face the dual challenge of limited funding and technological constraints for assessing deep-ore bodies where higher-grade deposits might exist.
Environmental clearances add another layer of complexity, often extending project timelines beyond what investors consider viable. The result: known deposits remain in the ground while import dependency grows.
Make in India, Defense Procurement, and Resource Strategy
India’s defense ambitions demand tungsten for armor-piercing ammunition, radiation shielding, and precision targeting systems. The Make in India initiative recognizes this reality, recently classifying tungsten as a strategic mineral requiring dedicated policy attention.
Mishra Dhatu Nigam Limited (MIDHANI) has begun developing specialized tungsten heavy alloys for defense applications, a move toward domestic capability that highlights both the strategic importance and current gaps in India’s tungsten ecosystem. Yet developing downstream processing capabilities while remaining import-dependent for raw materials creates its own vulnerabilities.
The path forward requires difficult choices. Revive domestic mining despite cost challenges? Secure long-term supply agreements with multiple international sources? Invest in recycling technologies that could recover tungsten from electronic waste and end-of-life defense equipment?
Key Takeaway: India’s tungsten dependency exposes strategic vulnerabilities in defense and aerospace sectors just as global competition for critical materials intensifies — making domestic resource development and supply chain diversification urgent national priorities.
Conclusion: Why Tungsten Will Remain Strategically Indispensable
Tungsten stands apart in a world increasingly defined by materials science, national security, and supply chain resilience, not for how much we use, but for how critical even small amounts can be.
A Material That Technology Cannot Replace
From the plasma-facing walls of fusion reactors to the vibration motor in your smartphone, tungsten operates where other materials simply cannot survive. Its extreme melting point enables fusion energy research that could power humanity’s future.
Its unmatched density creates armor-piercing capabilities that determine battlefield outcomes. Its unique properties make possible everything from precision surgical instruments to the X-ray systems that diagnose disease.
Strategic Applications Across Critical Industries
Strategic Applications of Tungsten Across Critical Industries
Industry | Strategic Significance | Supply Risk Impact |
---|---|---|
Aerospace | Satellite systems, heat shields | Mission-critical components |
Nuclear | Fusion reactor walls, medical shielding | No viable substitutes |
Defense | Kinetic penetrators, radiation protection | National security applications |
Medical | Surgical tools, imaging equipment | Patient safety and diagnostics |
Electronics | Filaments, semiconductor interconnects | Infrastructure reliability |
Recycling: A Strategic and Environmental Imperative
Yet tungsten’s scarcity creates profound vulnerabilities. With China controlling over 80% of global production and processing, nations worldwide face strategic dependencies in their most critical technologies.
s global supply chains tighten, recycling offers one of the most viable paths to resilience. Secondary tungsten — recovered from machining scrap and end-of-life components — already supplies more than 30% of refined tungsten globally. What makes this metal especially suited to circular strategies is that it can be recycled without degrading its performance, even for demanding applications in defense or medical technology.
“Tungsten can be recycled without losing quality — making it one of the few critical metals that truly fits into a circular economy.”
For countries without dominant mining positions, investing in tungsten recycling infrastructure not only reduces environmental impact but also strengthens strategic autonomy.
Looking Ahead: Demand, Innovation, and Global Leverage
This circular potential is especially relevant to countries like India, which import 95% of their tungsten requirements despite having domestic reserves — a pattern that reflects broader challenges in securing supply chains for strategic materials.
The metal’s irreplaceable role will only grow as emerging applications mature. Smart window coatings that reduce building energy consumption by 30-40%, nanowire sensors capable of operating at 300°C, and additive manufacturing techniques that create previously impossible geometries — all depend on tungsten’s extraordinary properties.
Countries recognize these realities. The inclusion of tungsten on critical mineral lists across the European Union, United States, Japan, and Australia signals an understanding: securing reliable access to this remarkable metal has become a matter of technological sovereignty.
Future demand will intensify as fusion energy programs advance, defense systems require more sophisticated materials, and precision manufacturing pushes performance boundaries. Nations that control tungsten supply chains will hold significant leverage over those that depend on imports for their most strategic technologies.
Key Takeaway: Tungsten’s combination of extreme properties makes it irreplaceable in applications that define technological leadership and national security. Supply chain concentration creates strategic vulnerabilities that nations are only beginning to address through alternative sourcing, recycling initiatives, and domestic resource development.
What steps should countries take to secure their tungsten supply chains while this strategic metal becomes even more critical to technological advancement?
FAQs
Q1. What makes tungsten unique among metals?
Tungsten has the highest melting point of any metal at 3,422°C, exceptional density of 19.25 g/cm³, and superior hardness, especially as tungsten carbide. These properties make it irreplaceable in applications requiring extreme heat resistance, concentrated mass, and wear resistance.
Q2. Where is tungsten commonly used in everyday life?
Tungsten is used in light bulb filaments, X-ray tube components, vibration mechanisms in smartphones, and cutting tools for machining. It’s also found in radiation shielding for medical equipment and high-performance vehicle components.
Q3. Why is tungsten important in aerospace and defense industries?
Tungsten’s high density and heat resistance make it crucial for radiation shielding in spacecraft, counterweights in satellites, and components in jet engines. In defense, it’s used in armor-piercing ammunition and kinetic energy penetrators due to its density and hardness.
Q4. How does tungsten contribute to nuclear power technology?
Tungsten serves as a plasma-facing material in fusion reactors due to its extreme heat resistance. It’s also used in reactor core components and radiation shielding in nuclear power plants and medical equipment.
Q5. What are some emerging applications of tungsten?
Emerging uses include tungsten nanowires for ultra-precise pH sensing, electrochromic coatings for smart windows, and additive manufacturing of complex tungsten components for aerospace and nuclear applications. These showcase tungsten’s expanding role in cutting-edge technologies.