Table of Contents
🔎 30-Second Summary
Cobalt is a silent powerhouse of the modern world—fueling the lithium-ion batteries in our devices, reinforcing jet engine components, and enabling life-saving cancer treatments. This article dives deep into cobalt’s unique chemistry, industrial applications, and its status as a Critical Raw Material.
You’ll explore how cobalt shapes energy storage, aerospace, medicine, agriculture, and electronics, while also examining the global supply chain risks and India’s strategic approach. From ancient pigments to cutting-edge technologies, discover why cobalt has become one of the most indispensable—and contested—elements of the 21st century.
How often do you use something powered by a metal you’ve never heard of?
You won’t find cobalt stamped on product labels, but this silvery metal quietly powers both the device in your pocket and the turbine blades spinning at 30,000 feet.
Cobalt is essential for lithium-ion batteries, but that’s just the start. Its magnetic strength, heat resistance, and catalytic activity also make it indispensable in jet engines, semiconductors, and cancer treatment equipment.
Global demand is rising fast. As of 2024, batteries account for 76% of cobalt consumption, with Bloomberg projecting a 47× surge in demand by 2030 compared to 2017. Cobalt makes up 10–33% of lithium-ion battery cathodes, particularly in advanced chemistries like LCO, NMC, and NCA.
The strategic pressure is mounting too. Over 70% of the world’s cobalt is mined in the Democratic Republic of Congo, and refining is dominated by China. Both the EU and US now list cobalt as a Critical Raw Material.
Despite being nearly invisible to consumers, cobalt is a cornerstone of modern infrastructure. From smartphones and satellites to wind turbines and electric vehicles, cobalt enables technologies that power the present, and shape the future.
What is Cobalt and Why It’s Unique
Cobalt, element 27 on the periodic table, sits between iron and nickel. This strategic position explains why it has such amazing properties that we can’t replace in many industries.
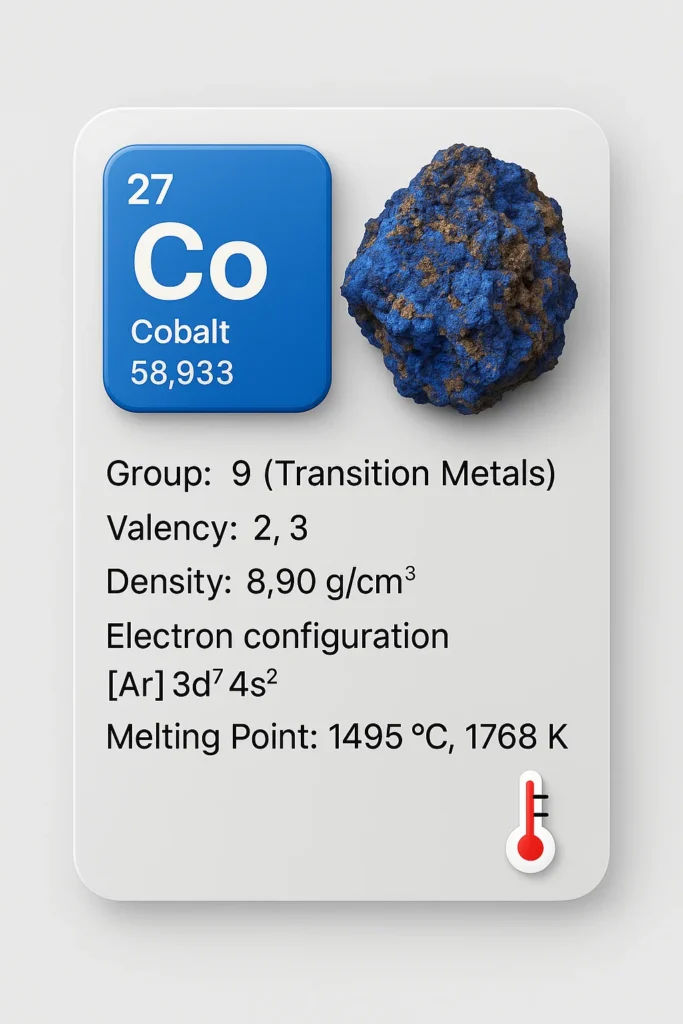
Atomic Traits and Redox Versatility
Cobalt exhibits remarkable atomic versatility, driven by its electronic configuration: [Ar] 3d⁷ 4s². This structure enables cobalt to adopt multiple oxidation states—most commonly +2 and +3, though it can range from -1 to +5 under special conditions. The Co²⁺ ion forms distinct pink-colored solutions in water, while Co³⁺ ions often yield green or blue compounds, depending on their ligands and environment.
What makes cobalt truly stand out is its redox flexibility. It can transition between oxidation states with minimal structural rearrangement—a trait that proves essential in lithium-ion battery chemistry. In cobalt-based cathodes, this redox behavior allows lithium ions to shuttle efficiently between electrodes during charge–discharge cycles.
With a moderate electronegativity of 1.88 (Pauling scale) and a compact atomic radius of 125 pm, cobalt strikes a balance between bonding reactivity and structural stability. These atomic characteristics make it uniquely suited for catalysis, electronics, and high-performance energy applications.
Ferromagnetism and Thermal Stability
Along with iron and nickel, cobalt is one of only three elements that remain magnetic at room temperature. But cobalt stands out with the highest Curie temperature, 1,115°C, meaning it retains magnetic properties even in extreme heat.
It also resists structural breakdown at high temperatures, making it ideal for gas turbines, jet engines, and other heat-intensive systems. This rare mix of magnetic and thermal resilience is why some technologies simply can’t function without cobalt.
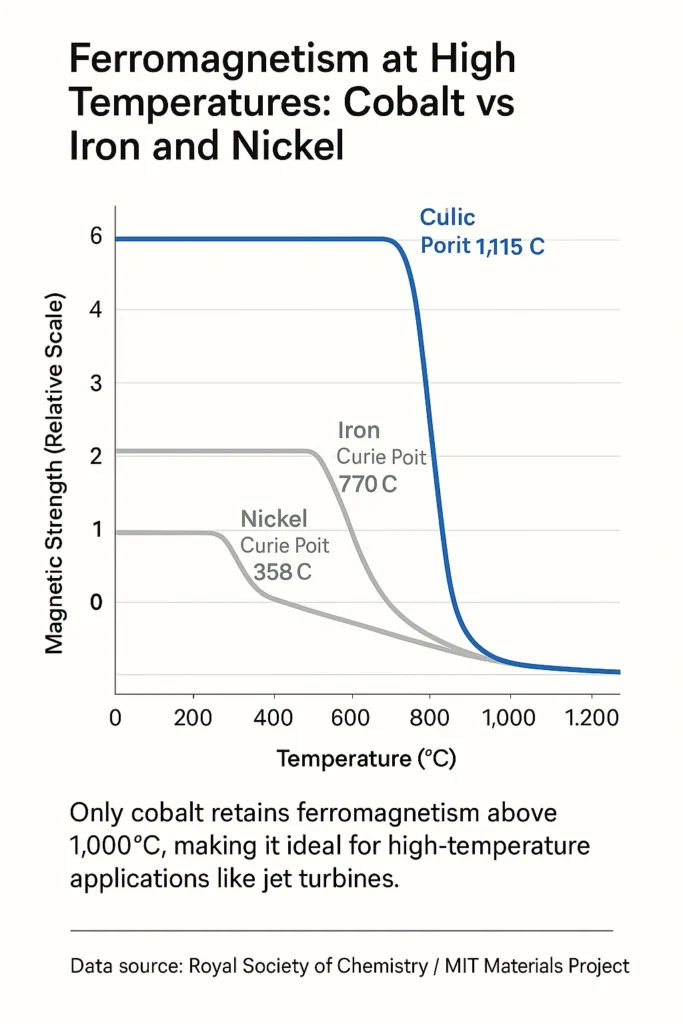
Industrially Relevant Compounds
Cobalt forms a range of compounds that serve essential roles across batteries, catalysts, agriculture, and materials science. One of the most critical is lithium cobalt oxide (LiCoO₂)—the preferred cathode material in consumer electronics due to its high energy density and thermal stability.
Another is cobalt oxide (Co₃O₄), used both as a ceramic pigment and a catalyst in oxidation reactions, particularly in energy and chemical industries.
Cobalt chloride (CoCl₂) is a classic humidity indicator: it shifts from blue when dry (anhydrous) to pink when exposed to moisture (hydrated), a dramatic color change leveraged in scientific and industrial settings.
Cobalt sulfate (CoSO₄) is widely used in electroplating and is also added to agricultural feeds as a precursor in vitamin B₁₂ production, crucial for animal health.
Lastly, cobalt carbonate (CoCO₃) acts as a versatile intermediate, used in manufacturing other cobalt salts, ceramic glazes, and as a nutritional supplement in livestock feed, highlighting cobalt’s often-overlooked role beyond high-tech applications. Even today, cobalt-based catalysts remain vital in refining petroleum, quietly sustaining the energy systems we still depend on.
Cobalt Compounds and Industrial Roles
Compound | Formula | Application | Notes |
---|---|---|---|
Lithium cobalt oxide | LiCoO₂ | Cathodes in electronics | High energy density, thermal stability |
Cobalt oxide | Co₃O₄ | Ceramics, catalysts | Oxidation reactions |
Cobalt chloride | CoCl₂ | Humidity indicators | Color change from blue to pink (hydrated) |
Cobalt sulfate | CoSO₄ | Electroplating, animal feed | Precursor for vitamin B₁₂ |
Cobalt carbonate | CoCO₃ | Ceramics, supplements | Intermediate compound |
Coordination Chemistry and Catalytic Behavior
Cobalt’s coordination chemistry might be its most interesting feature. It easily forms complex compounds with different ligands and can take many shapes from tetrahedral to octahedral. This flexibility lets cobalt take part in many catalytic processes.
For instance, cobalt-based catalysts drive hydroformylation reactions, which are used to convert alkenes into aldehydes, a foundational step in producing plastics, detergents, and pharmaceuticals at industrial scale.
In biological systems, cobalt porphyrin complexes resemble natural enzyme sites, helping mimic biochemical reactions. This makes cobalt useful in biomedical research and synthetic bioinorganic chemistry.
Cobalt’s ability to form stable complexes with oxygen makes it valuable in oxidation catalysis, especially in oil refining and environmental cleanup. These catalytic uses represent a growing area beyond the well-known battery applications.
Key Takeaway:
Cobalt is the backbone of modern battery technologies, providing structural, thermal, and electrochemical stability that no current alternative fully replicates—making it essential to the global energy transition.
Why Cobalt is Critical in Modern Technology
Cobalt serves as the life-blood of modern technology. Its unique properties make it essential in our increasingly electrified world, from smartphones to electric vehicles.
⚡ Cobalt’s Role in Energy Storage and Electric Vehicles
Lithium-ion batteries dominate cobalt’s use today, accounting for approximately 76% of global cobalt demand as of 2024. These power storage devices are found in electric vehicles, laptops, smartphones, and even medical devices. Cobalt improves battery performance in several key ways:
- Higher energy density packs more power into compact forms
- Better structural stability during charging cycles
- Stable voltage throughout battery discharge
- Faster charging capabilities
“Electric vehicles are only as green as the supply chains powering them, and cobalt sits at the heart.”
Battery demand is growing rapidly as countries pivot toward renewable energy. In fact, 50% of all cobalt mined today is used in rechargeable batteries, and Bloomberg projects cobalt demand could grow 4 fold by 2030 compared to 2017 levels.
The Environmental Protection Agency notes that transportation is the largest source of carbon emissions in the United States. As a result, the shift to electric vehicles, and the cobalt-based batteries that power them, has become a core strategy in fighting climate change.
Cobalt as a Critical Raw Material in the EU and US
Cobalt has been officially classified as a Critical Raw Material by both the European Union and the United States, reflecting its essential role in clean energy, heat-resistant materials, and industrial catalysts
But this recognition comes with a caveat: supply chains remain fragile. Over 70% of cobalt mining occurs in the Democratic Republic of Congo (DRC), while China refines nearly 60% of global output.
As part of its circular-economy plan, the EU is targeting 67% of its battery cobalt from recycled sources by 2050, aiming to reduce dependence and strengthen resilience.
With demand skyrocketing, cobalt now stands shoulder-to-shoulder with lithium, nickel, and copper in the global clean-tech race. Yet, securing ethical and stable supply chains remains one of the biggest challenges ahead.
Cobalt Uses in Battery Technology
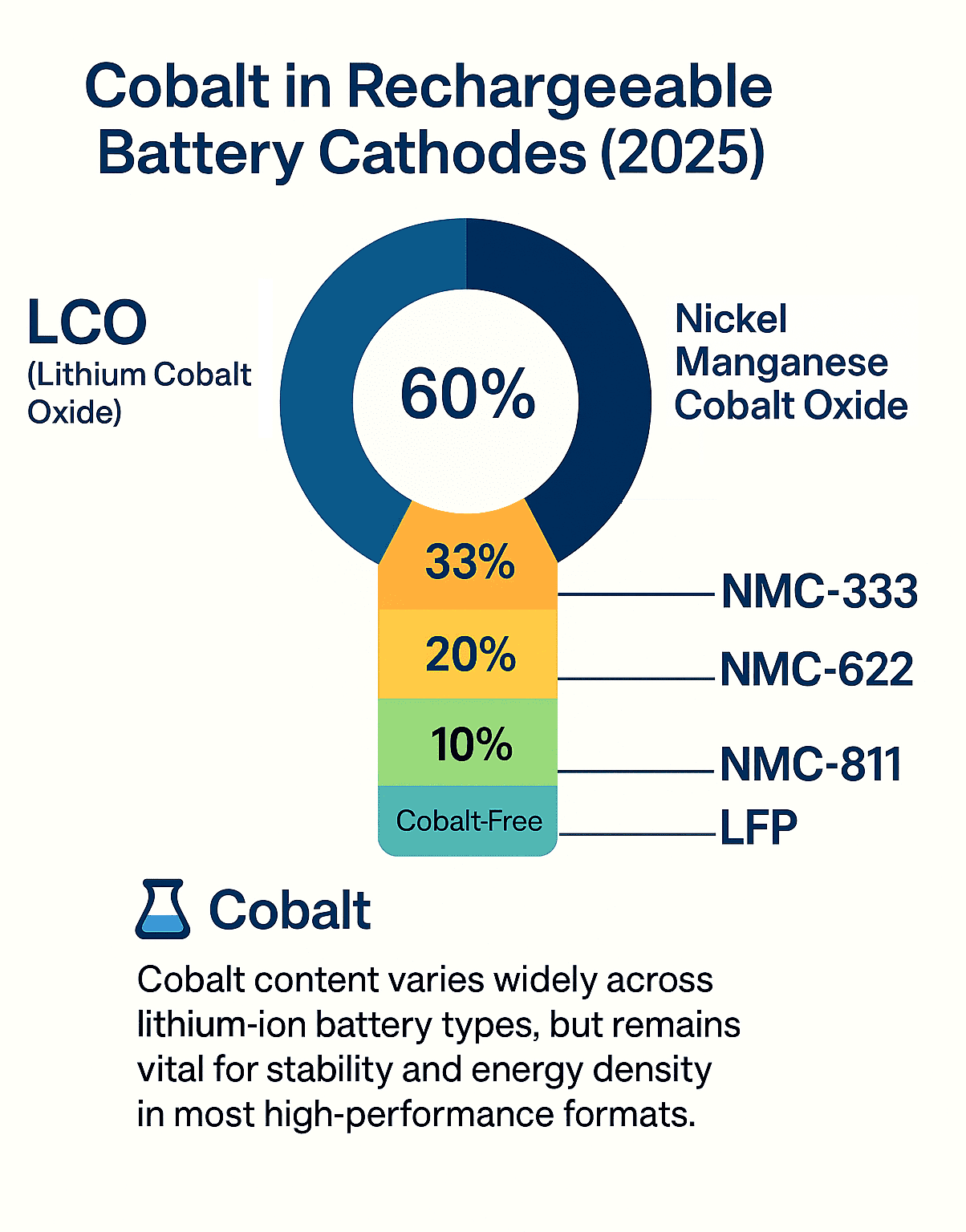
Batteries have become the biggest application for cobalt. This sector now accounts for 76% of global cobalt supply in 2024. This metallic element is a vital component in lithium-ion technology that powers everything from smartphones to electric vehicles.
Cobalt in Lithium-ion Cathodes: LCO, NMC, NCA
Lithium Cobalt Oxide (LiCoO₂ / LCO) is the original cobalt-based cathode and remains widely used in smartphones and laptops. It offers excellent stability over charge cycles and packs high energy into a compact volume, ideal for portable electronics.
Nickel Manganese Cobalt (NMC) batteries come in various blends like NMC-333 (equal parts) or NMC-811 (8:1:1). These blends balance energy density, safety, and cost. Nickel boosts capacity, manganese improves safety, and cobalt stabilizes the structure.
Nickel Cobalt Aluminum (NCA) cathodes—typically 80% nickel, 15% cobalt, 5% aluminum, deliver high specific energy, which makes them ideal for premium EVs. However, they come with trade-offs in terms of cost and safety.
The LFP Challenge: Performance vs. Cost Tradeoffs
Lithium Iron Phosphate (LFP) batteries have gained prominence as a cobalt-free alternative. Although they offer lower energy density, they provide several advantages:
- Reduced cost due to the absence of expensive metals
- Greater thermal stability and fire safety
- More abundant raw materials
- Improved environmental footprint
Originally popularised by Chinese manufacturers, LFP batteries have expanded into global markets and mass-market EVs. In 2021, LFP surpassed cobalt-based ternary chemistries with a 52% global market share by installed capacity. As of 2024, LFP holds 51% of the global battery market and continues to grow.
Manufacturers are also exploring organic materials as future cathode options, though these alternatives still fall short of cobalt’s conductivity and energy storage capacity.
Rising Demand and Supply Pressures in Battery Markets
Electric vehicles now consume 45% of the world’s cobalt. This figure is expected to rise as EV adoption expands. Market trends vary by region: about 90% of EVs in Europe and North America still rely on cobalt-containing batteries.
Battery-grade cobalt prices have fluctuated wildly, from $2,531 to $7,594 per kilogram over the last decade, reflecting both rising demand and supply instability. The Democratic Republic of Congo continues to supply over 70% of the world’s cobalt, creating geopolitical and ethical concerns.
To mitigate raw material pressure, the European Union aims to meet 67% of its cobalt needs for batteries through recycling by 2050. Cobalt reuse is emerging as a key strategy in building more sustainable and resilient battery supply chains.
“Electric vehicles now consume 45% of the world’s cobalt, and this number is only rising.”
The following comparison highlights cobalt content, key applications, and trade-offs across major lithium-ion battery chemistries.
Cobalt in Lithium-ion Battery Chemistries
Cathode Type | Cobalt % | Main Use | Strengths |
---|---|---|---|
LCO | 60% | Smartphones, laptops | Stability, volumetric capacity |
NMC-333 | 33% | EVs, energy storage | Balanced density and safety |
NMC-811 | 10% | Premium EVs | High energy, low cobalt content |
NCA | 15% | Tesla, high-end EVs | High specific energy |
LFP | 0% | Mass-market EVs | Safe, cheap, long life |
Key Takeaway: Cobalt’s role in lithium-ion cathodes like LCO, NMC, and NCA remains critical to achieving high energy density, long life, and thermal stability—factors LFP and organic chemistries still struggle to match.
Cobalt in Aerospace, Alloys, and High-Temperature Applications
Among the most critical cobalt uses are the high-temperature superalloys that keep jet engines running at extreme conditions. Cobalt’s real test comes in the extremes, where temperatures soar beyond 1,000°C and failure isn’t an option.
These specialized alloys tackle engineering challenges that would destroy conventional metals, particularly in aerospace systems, precision tools, and life-critical medical devices.
✈️ Superalloys That Power Modern Aviation
Cobalt-based superalloys form the backbone of modern jet propulsion, where turbine blades spin at 15,000 RPM while enduring temperatures that would melt copper. These materials maintain their structural integrity and mechanical properties under thermal stress exceeding 1,000°C, making them essential for turbine blades and combustion chambers where passenger safety depends on absolute reliability .
🔩 Alloy Chemistry and Heat Resistance
The engineering advantage lies in chemistry. Adding chromium above 20% creates exceptional oxidation and hot corrosion resistance. Cobalt superalloys achieve melting points above 1,300°C, significantly higher than most nickel-based alternatives, allowing them to function reliably in the hottest sections of jet engines.
These alloys don’t just survive extreme heat; they maintain dimensional stability and mechanical strength where other metals would soften, deform, or fail entirely. The result: jet engines that can operate safely for thousands of flight hours without catastrophic component failure.
⚙️ Stellite Alloys: Built for Wear Resistance
The Stellite family showcases cobalt’s mastery in wear-resistant metallurgy. By adding chromium, carbon, tungsten, and molybdenum, these alloys thrive in extreme industrial environments—where most materials fail.
What makes them stand out is not just their hardness but their ability to resist wear, corrosion, and deformation even under high temperatures. This resilience is crucial in sectors where downtime equals disaster.
Where standard alloys wear out in months, Stellite components can operate for years under identical conditions.
The metallurgical secret lies in carbide formation, especially Cr₇C₃ particles finely dispersed in a cobalt-rich matrix. This microstructure enhances mechanical stability while maintaining surface hardness at elevated temperatures. As a result, Stellite alloys are trusted in some of the most punishing industrial roles:
- Steam turbine erosion shields
- Precision cutting tools
- High-temperature extrusion dies
- Industrial valve components
- Food-grade processing equipment
Key takeaway: In extreme heat and high-stress environments, cobalt superalloys outperform most metals—proving essential in turbines, tools, and wear-resistant engineering.
Cobalt in Aerospace, Alloys, and High-Temperature Applications
**Alloy** | **Key Components** | **Primary Use** | **Strengths** |
---|---|---|---|
Superalloys | Co, Cr, Ni, Mo, W | Jet turbines, gas combustion engines | Heat resistance, structural integrity |
Stellite Alloys | Co, Cr, W, C, Mo | Valves, tools, extrusion dies | Wear & corrosion resistance |
Co–Cr Biomedical | Co, Cr, Mo, Ni (in trace) | Implants, dental prosthetics | Biocompatibility, fatigue strength |
🧬 Biomedical Engineering: Cobalt Inside the Human Body
Cobalt–chromium alloys have established themselves as the gold standard for medical implants requiring exceptional strength and biocompatibility. These alloys typically combine cobalt with 26–30% chromium, plus molybdenum and other precisely controlled elements .
🦴 Orthopedic Applications: Strength Where It Matters
These alloys perform exceptionally well in orthopedic devices thanks to their high stiffness, fatigue strength, and polished surface finish. These properties are critical in load-bearing joints such as artificial hips, knees, and shoulders, where mechanical durability and biological compatibility must coexist.
Cobalt implants don’t just restore movement—they restore quality of life
😁 Dental Prosthetics: Long-Term Performance in the Mouth
Beyond orthopaedics, cobalt–chromium alloys are widely used in dental prosthetics including crowns, bridges, and removable partial dentures. Their high biocompatibility, resistance to tarnish, and ability to hold a polished finish make them ideal for long-term oral use. Standards like ISO 22674 and EN ISO 9693 govern their use in dental frameworks.
Did you know? Standards like ISO 22674 and EN ISO 9693 ensure safety and consistency in cobalt–chromium dental frameworks.
⚙️ Manufacturing Methods: Precision Shapes Biocompatibility
Production techniques range from traditional casting and forging to advanced methods like selective laser melting (SLM), each influencing the alloy’s microstructure. The chromium content forms protective oxide layers that enhance corrosion resistance, critical for implants functioning safely for decades.
🧪 Trusted Grades: ASTM F75 and F799
Implant-grade variants like ASTM F75 and F799 have become industry benchmarks, offering long-term mechanical and biological performance inside the human body.
Key Takeaway:
Cobalt–chromium alloys have set the standard for medical implants, delivering biocompatibility, strength, and decades of clinical reliability.
Electronics, Magnets, and Catalysts: Cobalt’s Precision Applications
Cobalt’s versatility extends far beyond batteries and aerospace alloys. Electronics manufacturing, magnetic applications, and industrial catalysis reveal how this element’s unique properties enable precision technologies that demand both performance and reliability. These high-precision cobalt uses extend beyond batteries into magnetic sensors, semiconductors, and industrial catalysts.
Samarium-Cobalt Magnets: Extreme Temperature Champions
Samarium-cobalt (SmCo) magnets represent one of cobalt’s most sophisticated applications in modern technology. These permanent magnets exist in two primary compositions: SmCo5 and Sm2Co7. Maximum energy products range from 15-24 MGOe for SmCo5 and 20-32 MGOe for Sm2Co7, delivering exceptional magnetic strength in compact forms.
A side-by-side look at samarium-cobalt magnet variants reveals their strengths across temperature and energy density ranges.
SmCo Magnet Comparison (SmCo5 vs Sm2Co7)
Magnet Type | Composition | Max Energy (MGOe) | Use Case |
---|---|---|---|
SmCo₅ | Samarium\:Cobalt = 1:5 | 15–24 | Sensors, motors, precision devices |
Sm₂Co₇ | Samarium\:Cobalt = 2:7 | 20–32 | High-temp environments, aerospace |
SmCo magnets distinguish themselves through outstanding temperature stability, functioning efficiently between 523K and 853K while resisting demagnetization. This thermal resilience makes them indispensable for aerospace applications, precision sensors, generators, and medical equipment requiring sterilization at high temperatures .
Petrochemical Catalysis: Environmental Protection Through Chemistry
Cobalt serves a critical environmental function as a catalyst for removing sulfur from crude oil. This catalytic process prevents sulfur dioxide formation, a major contributor to acid rain, during fuel combustion. The process demonstrates how cobalt’s coordination chemistry enables large-scale environmental protection through industrial applications.
Semiconductor Revolution: The 22-Nanometer Breakthrough
Cobalt has emerged as a game-changing material in semiconductor manufacturing. Traditional materials reached their physical limits as transistors shrank below the 22-nanometer node.
Applied Materials discovered that replacing tungsten contacts and copper interconnects with cobalt significantly improves performance.
The performance gains are substantial: cobalt transistor contacts are 87% less resistive than tungsten alternatives. Cobalt provides better “wetting” of copper, minimizing electromigration and ensuring reliable connections. Applied Materials has called this “the most significant materials change to the interconnect in over 15 years”.
Cobalt rewrote the rules of semiconductor design, reducing contact resistance and enabling chips below the 22-nanometer barrier
Industrial Applications: Tools and Indicators
Cobalt powder serves as an essential binder in cemented tungsten carbide cutting tools throughout manufacturing industries. Studies show that varying cobalt content affects tool performance, with wear rate increasing alongside cobalt content at all cutting speeds. Cobalt chloride (CoCl₂·6H₂O) finds application as a humidity indicator, changing from pink (hydrated) to blue (dehydrated), alongside its use in catalyst preparation.
Key Takeaway: From magnetic sensors that operate at 580°C to semiconductor contacts that cut electrical resistance by 87%, cobalt enables precision technologies where performance margins define success or failure.
Cobalt in Medicine and Radiological Science
October 27, 1951 marked a turning point in cancer treatment. At the War Memorial Children’s Hospital in London, Ontario, doctors treated their first patient with Cobalt-60 therapy—an industrial metal turned life-saving technology. This breakthrough represented more than a new medical technique; it demonstrated how cobalt could transform global healthcare accessibility.
Cobalt in Medicine and Radiological Science
Application | Cobalt Form | Use Case | Impact |
---|---|---|---|
Radiotherapy | Cobalt-60 | Gamma radiation for cancer treatment | Effective even in low-infra settings |
Medical device sterilization | Cobalt-60 | Irradiation of surgical equipment | Sterile without chemical residues |
Radiopharmaceuticals | Cobalt-60 | Isotopic tracing in diagnostics | Track biological activity non-invasively |
Orthopedic implants | Co–Cr alloys | Hip/knee replacements | Strength, corrosion resistance |
Dental prosthetics | Co–Cr alloys | Bridges, dentures | Tarnish resistance, biocompatibility |
Cobalt-60 in Cancer Therapy and Medical Imaging
Cobalt-60 produces gamma radiation at two precise wavelengths: 1.17 and 1.33 MeV (high-energy rays used to zap tumors with millimeter precision), enabling targeted tumor destruction while minimizing damage to healthy tissue. The success stories speak for themselves, the first patient treated in Saskatoon was a 43-year-old woman with cervical cancer who lived beyond 90 years of age.
With Cobalt-60 in the clinic, patients saw breakthroughs such as:
- Effective palliation of distressing symptoms
- Prolonged life through sustained remissions, particularly in lymphomas
- Improved treatment outcomes with reduced patient discomfort
Diagnostic capabilities expanded as well. Cobalt-60 proves effective in detecting brain and lung metastases when conventional CT and MRI cannot visualize the damage. This dual capability, both therapeutic and diagnostic, underscores cobalt’s unique position in medical technology.
Radiopharmaceuticals and Sterilization Applications
Medical device sterilization represents Cobalt-60’s largest civilian application. About 98% of U.S. civilian radio-source activity uses Cobalt-60. The sterilization market is running near capacity and still growing at 5–7% per year.
These facilities ensure that surgical instruments and medical devices remain sterile and safe. The growth is driven by rising complexity in medical hardware and increasingly strict safety standards worldwide.
Cobalt-60 also functions as a radiotracer isotope, allowing physicians to track biological processes non-invasively, a capability that bridges diagnostic imaging with therapeutic applications.
Safety Profile and Clinical Applications
Cobalt-60 units dominated radiation therapy before modern linear accelerators became widespread. Although newer technologies have gradually replaced them, these cobalt-based units remain essential globally due to their reliability and simpler maintenance requirements.
Cobalt alloys have served medical applications for over seven decades, offering exceptional biocompatibility combined with mechanical strength and durability. These properties make them particularly valuable for implantable devices where long-term performance matters most.
Clinical research supports their safety profile. Studies indicate that exposure to cobalt alloys through clinically relevant routes presents negligible risks for adverse effects, supporting their continued use in medical applications.
Key Takeaway: Cobalt-60 transformed cancer treatment from experimental to accessible, while cobalt alloys enable long-term medical implants that improve quality of life for millions worldwide.
Cobalt in Agriculture and Animal Health
Cobalt might be better known for powering batteries and aerospace alloys, but its uses in agriculture and animal health are equally vital, playing a hidden yet powerful role in metabolism, soil biology, and livestock productivity.
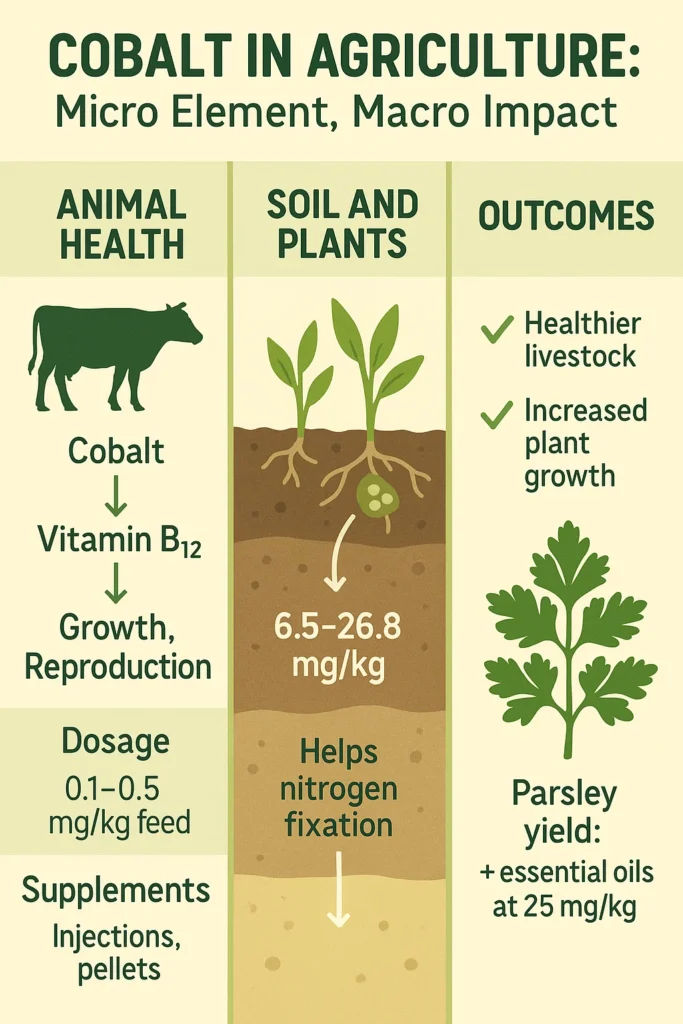
Cobalt’s Role in Vitamin B₁₂ Synthesis
Cobalt sits at the center of one of biology’s most essential molecules: cobalamin (vitamin B₁₂). In ruminant animals like cattle and sheep, microorganisms in the rumen ferment dietary cobalt to produce B₁₂, a process essential for converting nutrients into usable energy.
Yet the conversion efficiency is remarkably low: only 3–13% of dietary cobalt is turned into cobalamin by rumen bacteria. This biochemical bottleneck has significant consequences. Vitamin B₁₂ serves as a cofactor for key enzymes like methionine synthase and ethylmalonyl-CoA mutase (an enzyme vital for energy metabolism). Without enough cobalt, animals experience reduced methionine synthesis, diminished protein production, and broad metabolic dysfunction.
Cobalt deficiency manifests as reduced appetite, stunted growth, muscle wasting, and poor fertility, symptoms that directly affect animal health and farm economics.
“Only 3–13% of dietary cobalt is converted into vitamin B₁₂, yet this trace element controls growth, fertility, and metabolism in livestock.”
Strategic Supplementation in Animal Husbandry
To prevent deficiency, cobalt supplementation is now standard in commercial livestock management. Feed formulations typically include 0.1–0.2 mg/kg of cobalt per kilogram of dry matter. More intensive strategies include:
- Injectable vitamin B₁₂, effective for 6–8 weeks
- Intraruminal cobalt pellets, placed in the rumen and lasting 1–3 years
Diet composition matters. Grain-heavy diets tend to reduce microbial B₁₂ synthesis, while forage-rich diets enhance it. In one study, increasing cobalt from 0.1 to 0.5 mg/kg in sheep feed led to a 20-fold increase in vitamin B₁₂ production, a dramatic improvement in biological efficiency.
Soil and Fertilizer Relevance of Cobalt
Cobalt’s role doesn’t end with livestock, it also influences crop systems, especially in leguminous plants. Cobalt-deficient soils are common in highly weathered, leached regions, such as deep sandy terrains. For example, Egyptian soils show cobalt levels ranging from 6.5 to 26.8 mg/kg, a range that underscores the variability farmers must manage.
While plants themselves don’t need cobalt directly, legumes benefit indirectly: cobalt supports the Rhizobium bacteria in root nodules that drive nitrogen fixation. It also interacts with other micronutrients like iron, nickel, and zinc to maintain cellular balance.
Applied correctly, cobalt can enhance both yield and quality. In one experiment, parsley treated with 25 mg/kg of cobalt-enriched soil produced more biomass and essential oils, a rare win-win for plant growth and nutritional value.
Key Takeaway: Despite its low profile, cobalt is biologically indispensable — from livestock health to nitrogen fixation in soils, it underpins agricultural productivity and food security.
Cobalt in India: Demand, Policy, and Strategic Response
Cobalt uses in batteries, alloys, and radiological equipment are central to India’s evolving industrial and strategic roadmap.
Domestic Demand and Projected Growth
India’s clean-tech future will rely on one resource it barely produces: cobalt. Cobalt demand is expected to rise sharply in the coming decades, driven by the growth of electric mobility, renewable energy storage, and defence technologies. According to government estimates, cobalt consumption could reach 5,914 tonnes annually by 2047, primarily for lithium-ion batteries, aerospace-grade superalloys, and radiological medical devices. This estimate assumes current deployment trends; with accelerated electrification, the actual demand could climb significantly higher.
To understand where India stand, and where it must head, this table outlines key aspects of the nation’s cobalt landscape, highlighting current gaps and forward-looking strategies under government initiatives.
India’s Strategic Cobalt Outlook
Aspect | Current Status | Future Strategy |
---|---|---|
Domestic production | Negligible | Invest in secondary extraction and tailing recovery |
Imports | 90%+ from DRC via intermediaries | Diversify through KABIL + trade alliances |
Refining infrastructure | Underdeveloped | Build midstream capacity under Make in India |
Recycling potential | Untapped urban mining | Develop EV battery recovery & reuse pipeline |
Policy inclusion | Listed in 30 Critical Minerals (2023) | Integrated into National Mineral Security Framework |
Cobalt improves battery stability, enables high-temperature alloys, and supports radiological imaging, all core to India’s strategic ambitions. Its role in energy transition makes it a high-priority input under national initiatives like Make in India and the Production Linked Incentive (PLI) scheme for ACC batteries. The challenge lies not in usage, but in ensuring secure, long-term supply.
Import Dependence and Supply Chain Gaps
India currently lacks significant cobalt reserves or primary production. Nearly all domestic demand is met through imports, primarily sourced from the Democratic Republic of Congo, processed through intermediaries in China, Finland, and Belgium. In 2023, over 90% of India’s cobalt imports came through indirect or refined channels.
This dependence creates both geopolitical and economic vulnerabilities, especially as global demand surges and supply chains tighten. Relying on imports also exposes India to price volatility, particularly as battery metal prices spike during supply disruptions.
Moreover, India’s midstream processing and refining infrastructure remain underdeveloped. Without domestic capacity to extract, refine, or recycle cobalt, India risks being left behind in the race for critical mineral self-sufficiency.
“India’s cobalt challenge isn’t about demand, it’s about securing a stable, ethical, and domestic supply in a world of rising competition.”
Government Strategy and Policy Landscape
Recognising these supply-side vulnerabilities, the Indian government included cobalt in its official 2023 list of 30 critical minerals, acknowledging its strategic relevance across clean energy, defence, electronics, and medical sectors.
Externally, the government has tasked Khanij Bidesh India Ltd. (KABIL), a joint venture of NALCO, HCL, and MECL, with securing overseas assets for key minerals, including cobalt. As of 2024, KABIL has signed MoUs and conducted due diligence on multiple cobalt mining assets in countries like Australia, Argentina, and the DRC, signalling a shift toward long-term supply security.
Domestically, cobalt could be recovered as a by-product of copper and nickel refining, provided there is investment in tailings processing and extraction infrastructure. India’s growing battery and EV sectors also present an opportunity for cobalt recovery via urban mining and recycling.
[table “28” not found /]Strategic Roadmap for Resilience
To build a robust cobalt value chain, India’s long-term strategy must address both upstream and downstream bottlenecks:
- Develop refining capacity for cobalt and battery-grade precursors
- Invest in recycling infrastructure to reclaim cobalt from used EV batteries and electronics
- Secure international supply agreements through KABIL and strategic trade alliances
- Incentivise cobalt recovery from secondary sources and industrial waste streams
- Integrate cobalt planning into the National Mineral Security Framework
Key Takeaway: India’s future in clean energy and advanced manufacturing hinges on securing cobalt through international assets, domestic recovery, and circular economy strategies.
Sustainability, Supply Chain, and Future Outlook
Cobalt isn’t just a critical mineral, it’s a strategic chokepoint. Its supply chain is marked by intense geographic concentration, ethical controversies, and growing demand that outpaces recycling efforts. For resource-dependent economies like India, this creates a mix of vulnerability and opportunity.
“India’s cobalt challenge isn’t about demand, it’s about securing a stable, ethical, and domestic supply in a world of rising competition.”
Geographic Concentration: One Market, Few Players
The Democratic Republic of Congo (DRC) remains the world’s cobalt heavyweight, but Indonesia’s recent surge signals a shifting dynamic. Output in Indonesia jumped from 19,000 metric tons in 2023 to 28,000 in 2024 .
Yet this diversification is deceptive. The DRC’s new export quotas, following a four-month ban, now require local mineral processing, consolidating economic control. Even more striking, the DRC and Indonesia are exploring a joint cartel-like alliance to regulate global supply and stabilize prices.
Over 80% of the world’s cobalt may soon fall under coordinated control, making it one of the most geopolitically sensitive materials of our era.
This level of concentration mirrors Europe’s pre-war gas dependence, where a single policy shift can ripple across entire industries.
Human Rights and ESG: The Cost of Cobalt
Roughly 15–30% of the DRC’s cobalt comes from artisanal mines, involving over 150,000 informal workers , including an estimated 40,000 children. Working without protective equipment, these miners face extreme safety and health risks.
Environmental damage is another concern. Mining has reportedly destroyed millions of trees in cobalt-rich regions, harming both biodiversity and local livelihoods.
When ethical lapses enter the supply chain, the cost isn’t just human, it’s reputational, financial, and regulatory.
The ethical fallout is now a supply chain liability. Companies are investing in traceable, “clean” cobalt, driving up costs while trying to meet ESG mandates and avoid reputational damage.
Recycling: Not the Silver Bullet
Only 17% of global e-waste is currently collected for recycling , despite cobalt-rich batteries being a key source.
With proper infrastructure, up to 1,500 kilo tonnes of critical metals could be recovered over the next two decades.
But recycling alone can’t meet surging demand. The Cobalt Institute recommends broader policy measures, including:
- Mining codes that promote waste valorization
- Safe battery reuse protocols
- Consumer product standards for end-of-life recovery
Recycling is a vital piece, but not the whole puzzle.
Future Demand and the Road Ahead
India’s projected mineral needs by 2047 are staggering: 5,914 tons of cobalt, 20,845 tons of lithium, 18,599 tons of nickel, and 217,884 tons of graphite annually. And that’s based on today’s technologies.
Efficiency gains, like extending solar panel lifespans from 20 to 25 years, could reduce mineral demand by 30%. Yet such gains may be offset by expanding use in aerospace, defense, and digital infrastructure.
For resource-dependent economies, the choice is stark:
Accept import reliance, or invest in domestic refining, circular economy systems, and technology alternatives.
Key Takeaway: Cobalt’s supply chain is as strategic as the metal itself — navigating its ethical, geographic, and recycling challenges will define the next era of industrial resilience.
Conclusion
Cobalt is no longer just a commodity, it’s a linchpin in global technology systems, from powering digital life to enabling national security.
Its unmatched electrochemical and thermal properties ensure its continued role in high-performance batteries, medical devices, and aerospace-grade alloys, even as cobalt-free alternatives gain ground.
Yet, what makes cobalt indispensable also makes it risky. Its geographic concentration in a few countries, compounded by ethical sourcing issues and limited recycling infrastructure, transforms this element into a strategic variable, not just a raw material.
As governments reshape critical mineral strategies and industries adapt to sustainability demands, cobalt will remain at the centre of energy transitions, supply chain diplomacy, and materials innovation.
The countries that master its sourcing, processing, and substitution will gain not just industrial advantage, but geopolitical leverage in a resource-driven century.